While the competition in the production industry, which tries to respond to consumption, is increasing day by day, companies continue to improve their lines in order to produce a sufficient amount as well as prefer a package / packaging that will be the face of their brands. Although it seems simple, the packaging stage, which is one of the last point and most critical parts of production, is very important in terms of presenting the product to the customer in a carefully and carefully prepared package.
The packaging industry has turned to new and advantageous technologies in order to meet the packaging speed, quality, cost, etc. requirements of its customers in this competitive environment. At this point, Electric Actuators come into play with their cleaner, faster, smarter, more compact, less energy consuming and many more extra features, which quickly replace pneumatic applications. Electric actuators are flexible, easy to use, and economical motion modules.
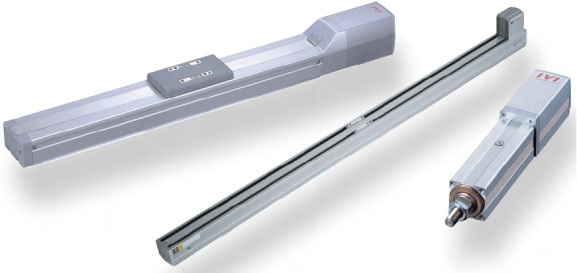
The packaging industry has turned to new and advantageous technologies in order to meet the packaging speed, quality, cost, etc. requirements of its customers in this competitive environment. At this point, Electric Actuators come into play with their cleaner, faster, smarter, more compact, less energy consuming and many more extra features, which quickly replace pneumatic applications. Electric actuators are flexible, easy to use, and economical motion modules.
RoboCylinder®s, which make the circular motion of servo or stepper motors linear with low friction mechanical systems, or SMAC actuators with moving coil based on magnetic force logic are examples of Electric Actuators. So what does these new technologies of the future bring us?
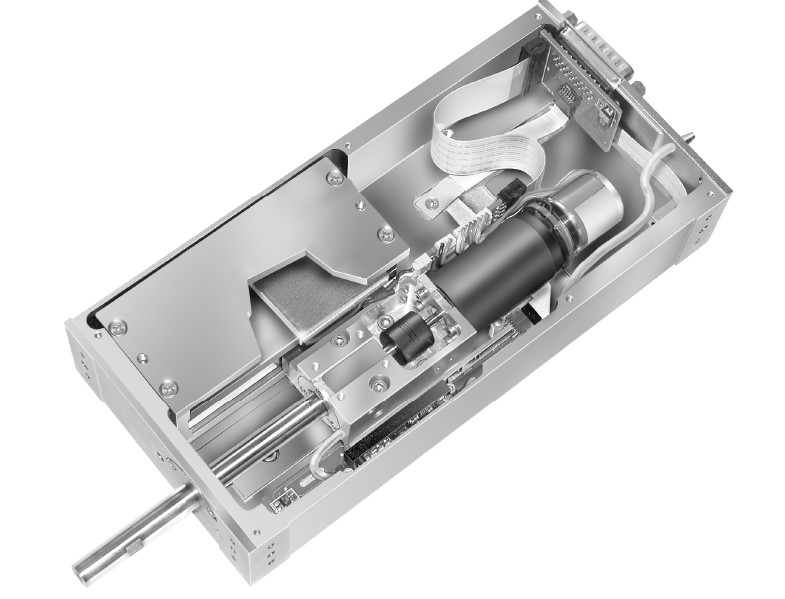
Positioning at any point with the built-in encoder without the need for a sensor – In both technologies, repeatability down to ±1microns can be easily achieved with unlimited different positions.
Mechanical adjustment requirements in product changes, which is one of the most time-consuming points for the end customer in packaging lines, are eliminated by the use of electric cylinders.
Thanks to the ability to save/program different stretches for products of different sizes and shapes to be packaged and to call them immediately, the set time between different products in the same packaging line is reduced to almost zero.
Acceleration can be adjusted numerically – Take-off and stop accelerations (ramps) can be adjusted independently of each other at the desired value. In this way, impact effects can be eliminated according to the sensitivity of the product, and time savings can be achieved by making sudden starts and stops. The life of the actuator is much longer as there is no bumping. Especially SMAC actuators allow maximum cycling per unit time, thanks to their acceleration up to 30G. (G: acceleration due to gravity =9800mm/s^2)
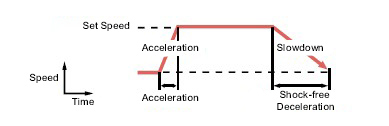
High Speeds and Ability to Change Speed on the Move – Electric cylinders can be varied in speed even while in motion. In this way, the total cycle time is shortened as much as possible by taking action faster or slower according to the status and behavior of the other work elements in the packaging system.
On the other hand, thanks to the high speeds of electric actuators, the number of products passing through the packaging lines per unit time can be increased significantly.
For example, at the end of a bottle filling line, products that are rejected by the camera level control must be removed from the line. However, due to the fact that the line is very fast, it is not possible to remove the bottle from the line by entering the flowing products without stopping, with standard actuators. In the application carried out with SMAC, it was possible to remove the bottles without any problems from the line moving at 500 bottles/minute.
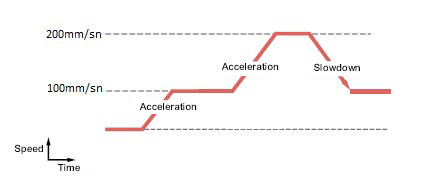
Thanks to the “Soft Land” feature – product contact with SMAC actuators can be achieved with low forces in a controlled manner. Therefore, damages such as breakage, damage, etc. are prevented. For example, in the process of removing the bottles from the line in the previous paragraph, thanks to this feature, the bottles were approached with the “slow approach” feature, then quickly removed from the line and their breakage was prevented and they could be reused.
“Constant Force (Push & Hold)” feature – The pressing force can be adjusted according to the position, or it can be determined as a fixed value. The advantage is that in case of conveyor speed fluctuations that may occur during packaging, when the actuator, which must descend between the packages, does not come across the package due to the fluctuation, more than the required pressure will occur, the actuator will realize this and stop the system in such errors.
Thanks to the same feature, it will be possible to separate different products flowing on the line at the same time according to their sizes, without using any sensors, cameras, etc. equipment.
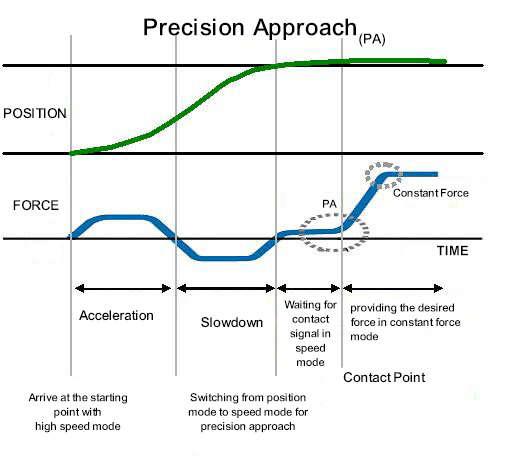