What is an Actuator?
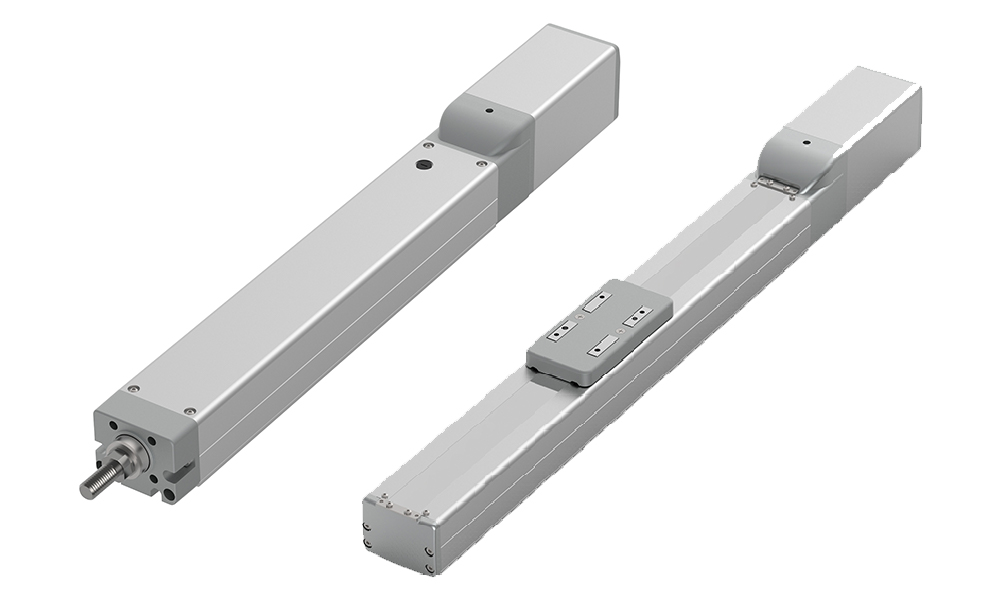
Figure 1- Electric Actuator
Actuator Types According to Energy Sources
Actuators are divided into three types according to their energy sources: hydraulic, pneumatic and electric. Each type has its own working principles and usage advantages. Let’s get to know these types closely.
1. Hydraulic Actuators
Hydraulic actuators work with pressurized hydraulic fluid. These systems take advantage of the incompressible nature of fluids and are generally preferred for lifting heavy loads. However, hydraulic systems require additional components such as fluid tanks, pumps and valves.
Fluid leaks that may occur in hydraulic hoses can both reduce efficiency and harm the environment. In addition, maintenance and installation costs are high. Another disadvantage of hydraulic actuators is that the pistons only work forward or backward; they cannot stop at an intermediate stroke value. This limits their areas of use.
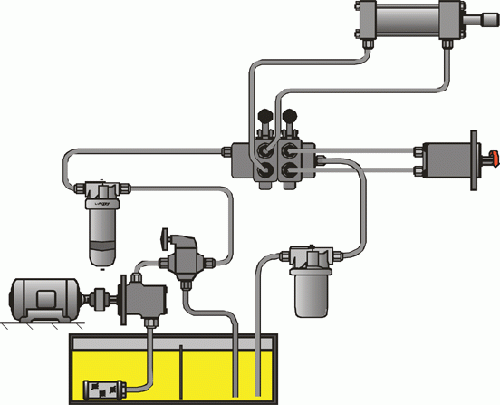
Figure 2- Working Principle of Hydraulic Systems
2. Pneumatic Actuators
Pneumatic actuators provide movement with compressed air. Additional systems such as compressor, air tank and conditioner are needed to use air. Although they have an advantage over hydraulic systems in terms of speed, the problem of not being able to stop in the middle stroke is also valid here.
Even in a leak-proof material, air leakage over time negatively affects efficiency. In addition, installation and maintenance costs are high. Although pneumatic systems are not as effective as hydraulics in heavy loads, they are frequently used in applications that require fast movement.
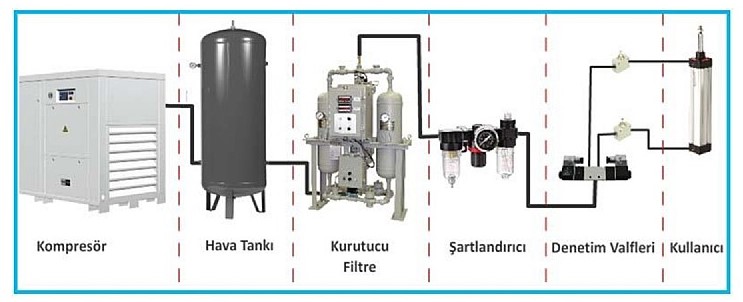
Figure 3- Working Principle of Pneumatic Systems
3. Electric Actuators
The most modern answer to the question of what is an actuator is hidden in electric actuators. Electric actuators provide movement with the help of a motor and ball gear. There is no need for a liquid tank or compressor as in hydraulic or pneumatic systems; only a controller is sufficient.
The biggest advantage of electric actuators is that they can work at the desired distance and acceleration throughout the stroke. Programming is completely up to the user, there is no risk of leakage and their efficiency is quite high. They also operate without noise, offer high precision and can react to unexpected obstacles. These features distinguish electric actuators from other types.
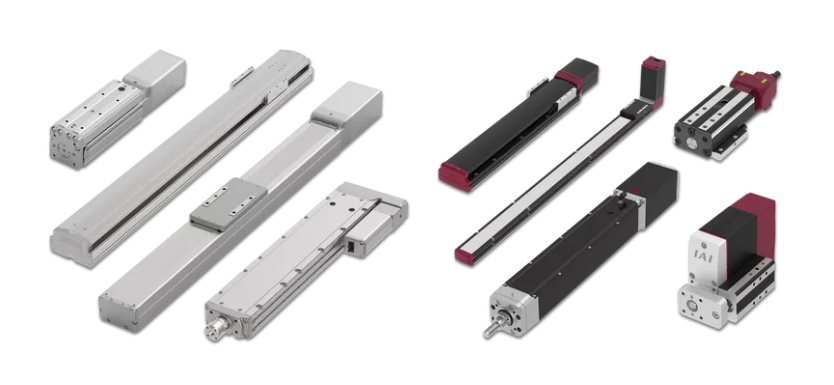
Figure – 4 Electrical Systems
Energy Efficiency in Electric Actuators
Energy Efficiency in Electric Actuators In pneumatic systems, 50% of the energy is lost as heat in compressors. The energy spent on work, including leaks, filter losses and exhaust, is only 14%. Similar losses are also experienced in hydraulic systems. However, these losses are minimal in electric actuators; 75% of the energy is converted to work. According to the Tokyo Institute of Technology reports, electric actuators are 5.36 times more efficient than pneumatic systems.
Similar energy losses to pneumatic systems are also present in hydraulic systems. Therefore, the highest efficiency obtained from actuator investments is in electric systems. The unit system used to indicate the amount of air produced per minute in compressors is CFM (Cubic Feet per Minute). Although each brand model compressor and the pneumatic actuators that use the compressed air produced by this compressor have different varieties, we can give an example based on an average value.
- Volume of the air chamber in the pushing direction == V1 = D2 ÷ 4 x π x h
- Volume of the air chamber in the pulling direction == V2 = (D2−𝑑2) ÷ 4 x π x h
- Volume of compressed air used in one cycle (push and pull) == V = V1 + V2
- Amount of compressed air used per minute == Vp = V x C
- The amount of air drawn from the atmosphere in one minute == Vatm = Vp x (𝑃 + 𝑃𝑎𝑡𝑚) ÷ 𝑃𝑎𝑡𝑚
- D = Cylinder inner diameter
- d = Piston rod diameter
- h = The amount of linear extension
- C = Number of cycles (push-pull) per minute
- P = Air pressure supplied to the cylinder
- Patm =Atmospheric pressure
- 1 m3 / minute = 35.3 CFM
- 1 HP = 2.5 CFM 6bar
- 1 HP = 0.746 kW
We can use the value 0.75 as the pneumatic transmission multiplier.
Let’s look at the values through an example:
Cylinder inner diameter D = 25 mm | V1 = (0.0252 ÷ 4) x 3.142 x 0.3 =1.47 x 10-4 m3 |
Piston rod diameter d = 10 mm | V2 = (0.0252−0.0102) 4 x 3.142 x 0.3 = 1.24 x 10-4 m3 |
Air pressure supplied to the cylinder P = 6 bar | V = V1 + V2 = 2.71 x 10-4 m3 |
The amount of extension h = 300 mm | Vp = 2.71 x 10-4 x 30 = 8.13 x 10-3 m3 |
Number of cycles C = 30 cycles / minute | Vatm = 8.13 x 10-3 x (6+1) ÷1 = 5.69 x 10-2 m3 = 2CFM |
Power consumed by the compressor | Güç = 0.746 x 2 (0.75 x 2.5) = 0.79kW |
2000 hours of electricity cost (250 days at 8 hours per day = for businesses operating only on weekdays) | 0,79kW x 2000h x 3.569785TL = 5640.2603TL |
7200 hours of electricity cost (for businesses operating 24 hours a day for 300 days = 24/7) | 0,79kW x 7200h x 3.569785TL = 20304.93708TL |
Table- 1 (Based on the 2022 electricity unit industrial price.)
Let’s compare the pneumatic actuator in Table -1 with the electric actuator of the IAI brand, code RCP6-RA7C-WA-56P-16 300, which can handle a similar load. During the test, a counterload of 200N was applied to both the pneumatic and electric actuators.
Model | RCP6-RA7C-WA-56P-16-300 |
Encoder | Battery-free Absolute Encoder |
Gear Step | 16 mm |
Stroke | 300 mm |
Speed | 700 mm/s |
Load Capacity Horizontal | 50 kg |
Load Capacity Vertical | 8 kg |
Maximum Compression Force | 273 N |
Sensibility | 0.01 mm |
Table- 2
To simulate a business that operates only 8 hours a day on weekdays, both pneumatic and electric actuators were operated for 2000 hours. The graph of the simulation is as follows.
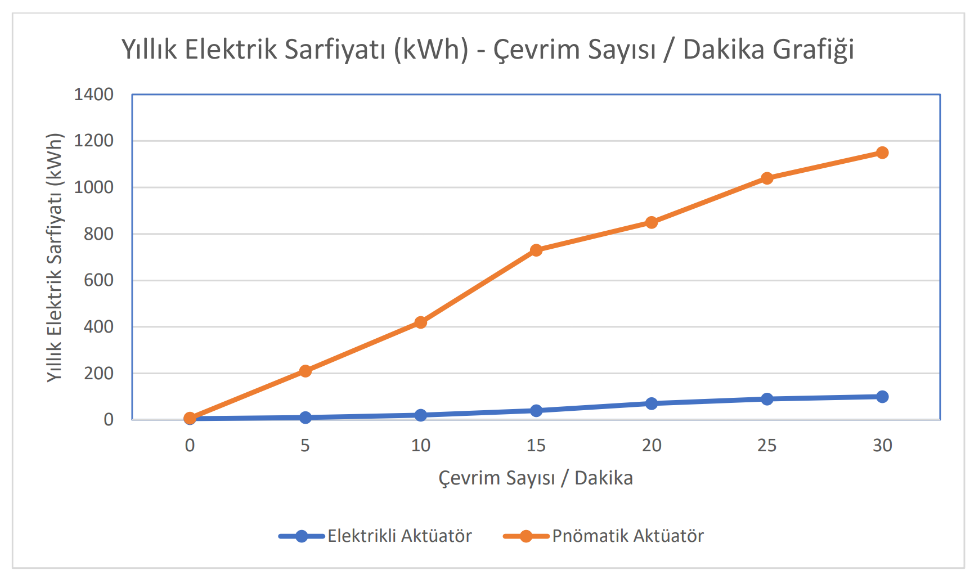
Graph – 1
Example Calculation: Pneumatic Actuator vs Electric Actuator
A pneumatic actuator, when cycling at 30 cycles per minute, uses 2 CFM of air and consumes 1,100 kWh of energy annually. An electric actuator operating under the same conditions uses only 100 kWh. The 11-fold difference clearly shows why electric actuators are preferred.
Areas of Use of Actuators
- Hydraulic Actuators: Construction machinery, cranes and heavy industry.
- Pneumatic Actuators: Fast assembly lines and light load applications.
- Electric Actuators: Robotics, automation systems and precision machinery.
Why Choose Electric Actuators?
After answering the question, “What is an actuator?” it becomes clear: Electric actuators outperform other types in terms of efficiency, low cost and flexibility. Offering energy savings and high accuracy, these systems are indispensable in modern industry.